Observing safety measures for polyurethane spray foam installation should be the priority for every job regardless of size. Being well versed in using polyurethane spray foam machinery and components will ensure a safe working environment and avoid any hazards.
Here are the key safety measures for polyurethane spray foam installation:
1. Training and Awareness
- General Safety – Training workers is absolutely crucial. Before operating any machinery, spray foam workers must know all general safety procedures such as proper use of PPE and emergency response actions. We will go into more detail in the points, below.
- Equipment Operation – Spray foam insulation and coating machinery manufacturers and distributors must ensure that workers are trained in the safe and proper operation of foam spray proportioners, hoses and spray guns including startup, operation and shutdown procedures. For more information, refer to the product manual for your machine and components.
2. Equipment Maintenance
- Regular Inspections – Regularly inspect spray foam equipment for wear, leaks, and proper functioning. As a built-in safety measure, PMC proportioners are equipped with a double acting piston displacement pump, ensuring that the same amount of material is moved on both sides (A pump and B pump) at the same time. This is crucial not only for chemical safety but for proper application.
- Preventative Maintenance – Perform routine maintenance as recommended by the manufacturer.
- Make Repairs Immediately – Address any equipment malfunctions or damage promptly to prevent accidents. Contact a PMC authorized distributor for repairs and tech support.
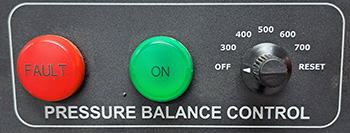
ensures the safe 1:1 ratio of spray foam chemicals
3. Hazard Communication
- Safety Data Sheets (SDS) – Another safety measure is to provide access to Safety Data Sheets for all chemicals used, and ensure workers understand the hazards and first aid measures. Carefully read and follow the SDS provided by your supplier. A few are listed here:
- Labeling – Ensure all containers are properly labeled with hazard information.
4. Personal Protective Equipment (PPE)
- Respiratory Protection – Use a National Institute for Occupational Safety and Health (NIOSH)-approved respirator suitable for protection against organic vapors, particulates, and isocyanates. Full-face respirators are recommended for outdoor applications, and powered air-purifying respirators (PAPRs), commonly referred to as fresh air supplies, are recommended for indoor or closed space applications. Respirator Fit Testing is a must.
- Eye Protection – Goggles or Full-Face Shields are required. Wear chemical splash goggles or a full-face shield to protect against splashes and airborne particles. These are included in fresh air supplies, as the hood in these systems will fully cover the face and head.
- Skin Protection – It is necessary, even in the summer heat, to protect all parts of your body from exposure to foam spray.
- Gloves: Use chemical-resistant gloves, such as nitrile or neoprene, to prevent skin contact with chemicals
- Coveralls: Wear disposable coveralls or a long-sleeved shirt and long pants made of materials resistant to chemical penetration. The standard white hazmat is the way to go since it will protect your clothes as well as your skin.
- Boots: Wear chemical resistant boots to protect feet from spills.
- Learn more about PPE here.
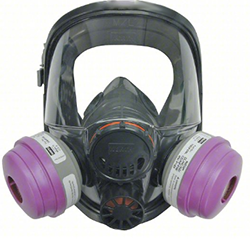
5. Ventilation and Work Area Controls
- Adequate Ventilation – mechanical ventilation such as fans or exhaust systems will ensure proper ventilation in the work area, especially in enclosed spaces. This helps disperse fumes and maintain air quality.
- Air Monitoring – Regularly monitor air quality to ensure concentrations of hazardous substances remain below permissible exposure limits (PELs).
- Isolation of work area – Set up physical barriers to isolate the spray area and prevent unauthorized access.
- Signage – Post warning signs around the work area to inform others of the hazards and restricted access.
6. Safe Handling and Storage of Chemicals
- Storage – **Please refer to your supplier’s recommendations for additional information**
- Temperature control: Store isocyanates and polyol resins at recommended temperatures to prevent degradation and ensure proper application.
- Secure Containers: Keep containers tightly closed when not in use and store them in a well-ventilated area away from sources of ignition
- Mixing and Dispensing: Follow manufacturer guidelines for mixing and dispensing chemicals. Use equipment designed for handling polyurethane foam components.
- Spill Control: Have spill control kits readily available and ensure workers are trained in proper spill response procedures.
- Use Caution with Pressurized Fluids: Do not open any connection of perform maintenance on any components until the pressure has been completely eliminated
7. Emergency Preparedness
- First Aid Kits: Maintain well-stocked first aid kits on-site and ensure workers know their locations.
- Emergency Eyewash and Showers: Provide emergency eyewash stations and safety showers in areas where chemicals are used.
- Evacuation Plan: Develop and communicate an emergency evacuation plan, as well as other emergency procedures.
- Incident Reporting: Establish procedures for reporting and responding to accidents, spills, or exposures.
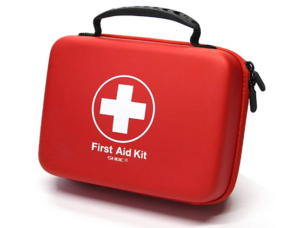
By following these safety precautions, workers can minimize their exposure to hazardous chemicals and ensure a safer work environment when using PMC polyurethane spray foam machinery. If you have any questions, you can contact us or an authorized distributor near you.