The future of spray foam is outstanding. The industry is growing rapidly, nearly doubling its market size over the past ten years. Ongoing research and development have led to advancements in machine design and efficiency, as well as improved plural component chemical performance. With skilled contractors, manufacturers, and distributors at the ready, this industry is poised to meet growing market demands and reduce environmental impact for decades to come.
According to The Business Research Company, a leading provider of actionable market insights, the spray foam insulation market is projected to experience significant growth in the coming years, reaching an estimated $3.18 billion by 2034 with a compound annual growth rate (CAGR) of 6.7%. This expansion is driven by factors such as:
- Increased construction activity
- Greater awareness of energy-efficient insulation solutions
- Rising demand for environmentally friendly materials
- Stricter regulations are aimed at reducing carbon emissions in the building sector.
New Developments to Advance the Spray Foam Industry
Developing innovative solutions is paramount to moving the spray foam industry forward. Such innovations encompass improving machine technology as well as the plural component chemicals. After all, spray foam equipment is only as good as the quality of foam it sprays.
One such chemical innovation is Huntsman Building Solutions’ introduction of Icynene Xpress 55, an open-cell spray foam for unventilated crawl spaces and attics. It is noteworthy for its fire-retardant properties, reducing the need for an ignition barrier and superior insulation providing an R-value of R-3.7 at 1” and R-13 at 3.5”. As with all spray foam, it offers the added benefit of reducing environmental pollution and noise.
Machine technology needs to meet the demands of a rapidly growing industry. The PMC Premier Mach 2 is the first of its kind, a patent-pending dual gun proportioner that outputs 40 lbs./minute and supports two size 02 or equivalent chamber spray guns. The single pump line and heater pull only 77 amps, allowing one machine to do the job of two. Beyond the dual gun capacity is the data reporting, recording, and remote access technology. Innovations such as this improve productivity while reducing carbon footprint.
Spray Foam Industry By The Numbers (courtesy of TBRC)
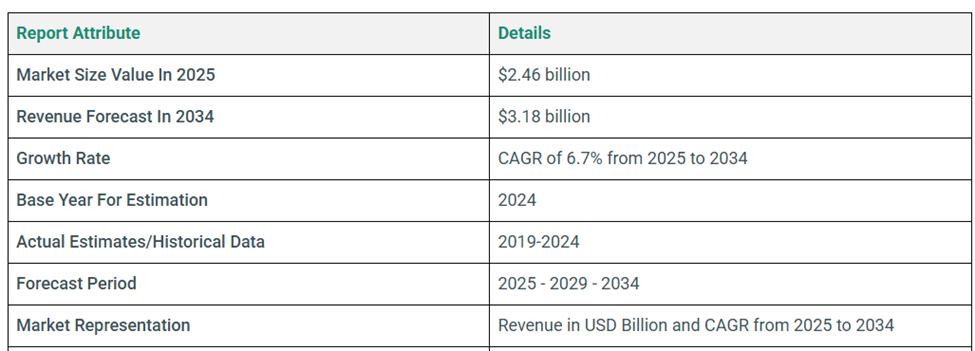
Are the Advantages Worth the Cost?
Nationally, installing spray foam insulation in an attic could cost the consumer between $2 and $5 per foot. Additional factors such as the type of foam, local labor costs, and the project scope could sway the cost above or below this estimate. Overall, it is accurate to say that spray foam insulation bears a higher installation cost than conventional fiberglass insulation. However, the advantages it provides pay for themselves over time.
- Efficiency: Spray polyurethane foam has an airtight seal and a high R factor, which reduces energy loss and lowers monthly energy consumption, resulting in lower utility bills. In addition, it can be applied in hard-to-reach places, ensuring a complete seal of your space.
- Long-Lasting Durability: plural component spray foam will not decompose or break down over time. Other forms of insulation may settle or succumb to environmental damage, but foam maintains its structure and integrity over time.
- Increase comfort in your home: Spray foam can prevent mold and mildew and improve air quality in your home. It can also reduce outdoor noise and deter pests.
Recession Proof Industry
The spray foam industry is experiencing remarkable growth, driven by increasing demand for energy-efficient, durable, and environmentally friendly insulation solutions. The demand for more spray foam insulation contractors is needed to meet the growing need.
With the current cost of housing at an all-time high, many homeowners are choosing to remodel rather than relocate. Improving an older home’s energy efficiency is a worthwhile investment leading to innumerable opportunities for spray foam installers.
In new home construction, the US Department of Energy recommends a Whole House System approach to home design to achieve ultra-efficient and Zero Energy Ready Home design. As such, they have outlined the requirements for R-factor in new home insulation. Furthermore, Zero Energy Ready Homes are being built throughout the country and will be mandatory for all new home construction in California starting in 2025.
Meeting the Demand
Machine technology and chemical formulations will continue to propel the industry forward. Equipment and chemical manufacturers are rising to the challenge of responding to market needs with enhanced performance, efficiency, and sustainability of their products.
Continued improvements to spray foam machinery, guns, hoses, pumps, and chemicals, coupled with adequately trained and knowledgeable insulation contractors will see the industry through this growth spurt and beyond.
The spray foam industry is here to stay.